Function of Welding Robots
1. Position finding function. The end positioning function is indispensable for workpieces with large tolerances or poor assembly accuracy. The positioning device has a wire package that can generate tens of volts. Position finding is the momentary short circuit caused by the welding wire contacting the workpiece, that is, the robot system finds the three-dimensional coordinates of the point of the actual workpiece weld. In this way, the robot system detects multiple points and calculates the deviation value based on these points. , Use the deviation value to modify the position data of the originally taught weld seam, so as to obtain the position of the actual weld seam starting point.
2. Arc tracking function. During the welding process of the welding robot, due to the influence of various factors in the welding environment, such as processing error, fixture installation accuracy, surface condition, spatter and thermal deformation of the workpiece, the actual welding path deviates from the original teaching path, resulting in Welding quality has deteriorated or even failed. The arc tracking function is to measure the changes in the welding current during the welding process, and then the robot automatically calculates the data generated by the arc swing during the welding process to obtain the exact position of the weld and correct the welding path.
3. Arc restart function. After the workpiece is extinguished due to unexpected circumstances, it can carry out the arc starting action of the equipment times in advance, thereby reducing the pause time and improving the production efficiency.
4. Welding torch recovery function. The torch recovery function is a function that automatically corrects the deviation of the tip position of the welding torch wire in a short time. By using this function, the downtime can be shortened and stable welding quality can be obtained.
5. Database function. The database includes a welding expert database and a database compiled by the user. The powerful expert database includes the weld form of the workpiece to be welded and the corresponding process parameters. Calling the expert database greatly simplifies teaching workload and improves work efficiency.
Users can also call or modify the process parameter table according to their own process requirements, so as to achieve the desired effect.
6. Various forms of weaving welding function. For medium and thick plates, it is generally necessary to swing during manual welding. At this stage, the welding robot also provides various forms of swing welding functions, such as: SIN swing, circular swing, and eight-shaped swing. In the setting of swing parameters, the user can define the swing amplitude, frequency, and stop time at the end of the swing by himself.
7. Anti-collision function. The collision function refers to the function that can prevent the various joints of the robot from colliding with the workpiece or the positioner due to the unreasonable operation. In addition, according to the actual welding conditions, you can select the positioner idling avoidance function, the regeneration temporary stop automatic recovery function, and the nozzle contact avoidance function.
LH WELDING ROBOT
6 axis robot
Support 2~5 external axis control
Dedicated welding software pack
Repetition accuracy: 0.05mm
Payload: 6kg
Arm motion radius: 1500mm,1850mm,2100mm
Equipped with a full welding system
Support Modbus TCP/IP,RTU
Laser welding, argon arc welding,…
Laser automatic welding seam tracking sensor optional
Support carbon steel,stainless steel,galvanized plate,aluminium alloy welding,
We Supply You
A Complete Robot With Welding Source&Accessories
This is a complete welding robot that comprises robot arm,robot controller, teaching pendant,ultra-low splash welding source MIG or TIG 300A,anti-collision welding torch, wire feeder, wire feeder hose, wire rack,two reservation boxes, isolation transformer.
Welding Robot(dustproof) LH1500 – B- 6
Rated payload | 6KG | |
Work radius | 1500mm | |
Structural style | Series connection | |
Number of axis | 6 | |
Repetitive accuracy | ±0.05mm | |
Max operation range | Axis 1 | ±165° |
Axis 2 | +135°/-75° | |
Axis 3 | +78°/-76.5° | |
Axis 4 | ±360° | |
Axis 5 | ±115° | |
Axis 6 | ±450° | |
Max speed | Axis 1 | 148°/sec |
Axis 2 | 148°/sec | |
Axis 3 | 150°/sec | |
Axis 4 | 222°/sec | |
Axis 5 | 222°/sec | |
Axis 6 | 360°/sec | |
Net weight | ≈120kg | |
Installation | Ground/rack/ceiling | |
Ambient temperature | -20℃~80°C |
Application
Automobile, hardware doors and windows, construction machinery, mining machinery, railway locomotive, electrical furniture and other industries
LH1500-B-6 robot is specially used in the welding field. It is a robot developed for more harsh field environment. This product has a larger installation area and stable structure, as well as a fully sealed structure with one shaft, which effectively prevents some welding slag from damaging the robot wire.
Welding Robot(dustproof) LH1850- B- 6
Rated payload | 6KG | |
Work radius | 1850mm | |
Structural style | Series connection | |
Number of axis | 6 | |
Repetitive accuracy | ±0.05mm | |
Max operation range | Axis 1 | ±165° |
Axis 2 | +135°/-75° | |
Axis 3 | +78°/-76.5° | |
Axis 4 | ±360° | |
Axis 5 | ±115° | |
Axis 6 | ±450° | |
Max speed | Axis 1 | 148°/sec |
Axis 2 | 148°/sec | |
Axis 3 | 150°/sec | |
Axis 4 | 222°/sec | |
Axis 5 | 222°/sec | |
Axis 6 | 360°/sec | |
Net weight | ≈120kg | |
Installation | Ground/rack/ceiling | |
Ambient temperature | -20℃~80°C |
Application
Automobile, hardware doors and windows, construction machinery, mining machinery, railway locomotive, electrical furniture and other industries
LH1850-B-6 robot is specially used in the welding field. It is a robot developed for more harsh field environment. This product has a larger installation area and stable structure, as well as a fully sealed structure with one shaft, which effectively prevents some welding slag from damaging the robot wire.
LH2100-B-6
Welding Robot (dustproof)
Rated payload: 6KG
Work radius: 2100mm
Structural style: Series connection
Number of axis: 6
Repetitive accuracy: ±0.05mm
Max operation range:
Axis 1 ±165°
Axis 2 +135°/-75°
Axis 3 +78°/-76.5°
Axis 4 ±360°
Axis 5 ±115°
Axis 6 ±450°
Max speed:
Axis 1 148°/sec
Axis 2 148°/sec
Axis 3 150°/sec
Axis 4 222°/sec
Axis 5 222°/sec
Axis 6 360°/sec
Net weight 235kg
Installation: Ground/rack/ceiling
Ambient temperature: -20℃~80°C
Applications for Automobile, hardware doors and windows, construction machinery, mining machinery, railway locomotive, electrical furniture and other industries
LH2100-B-6 robot is specially designed for welding field. It is a robot developed by the company based on the existing LH1850-B-6 for customers’ more severe field environment. Compared with the previous product, this product has a larger installation area and stable structure, as well as a shaft full sealing structure, which effectively prevents the damage of some welding slag to the robot wire.
Welding Robot(hollow) LHZ1500 – B- 6
Rated payload | 6KG | |
Work radius | 1500mm | |
Structural style | Series connection | |
Number of axis | 6 | |
Repetitive accuracy | ±0.05mm | |
Max operation range | Axis 1 | ±165° |
Axis 2 | +135°/-90° | |
Axis 3 | +90°/-90° | |
Axis 4 | ±360° | |
Axis 5 | +115°/-140° | |
Axis 6 | ±450° | |
Max speed | Axis 1 | 148°/sec |
Axis 2 | 148°/sec | |
Axis 3 | 150°/sec | |
Axis 4 | 222°/sec | |
Axis 5 | 222°/sec | |
Axis 6 | 360°/sec | |
Net weight | ≈120kg | |
Installation | Ground/rack/ceiling | |
Ambient temperature | -20℃~80°C |
Application
Automobile, hardware doors and windows, construction machinery, mining machinery, railway locomotive, electrical furniture and other industries
LHZ1500-B-6 robot is specially used in the welding field. It is a robot developed for more harsh field environment. This product has a larger installation area and stable structure, as well as a fully sealed structure with one shaft, which effectively prevents some welding slag from damaging the robot wire.
Welding Robot(hollow) LHZ1850- B- 6
Rated payload | 6KG | |
Work radius | 1850mm | |
Structural style | Series connection | |
Number of axis | 6 | |
Repetitive accuracy | ±0.05mm | |
Max operation range | Axis 1 | ±165° |
Axis 2 | +135°/-90° | |
Axis 3 | +90°/-90° | |
Axis 4 | ±360° | |
Axis 5 | +115°/-140° | |
Axis 6 | ±450° | |
Max speed | Axis 1 | 148°/sec |
Axis 2 | 148°/sec | |
Axis 3 | 150°/sec | |
Axis 4 | 222°/sec | |
Axis 5 | 222°/sec | |
Axis 6 | 360°/sec | |
Net weight | ≈120kg | |
Installation | Ground/rack/ceiling | |
Ambient temperature | -20℃~80°C |
Application
Automobile, hardware doors and windows, construction machinery, mining machinery, railway locomotive, electrical furniture and other industries
LHZ1850-B-6 robot is specially used in the welding field. It is a robot developed for more harsh field environment. This product has a larger installation area and stable structure, as well as a fully sealed structure with one shaft, which effectively prevents some welding slag from damaging the robot wire.
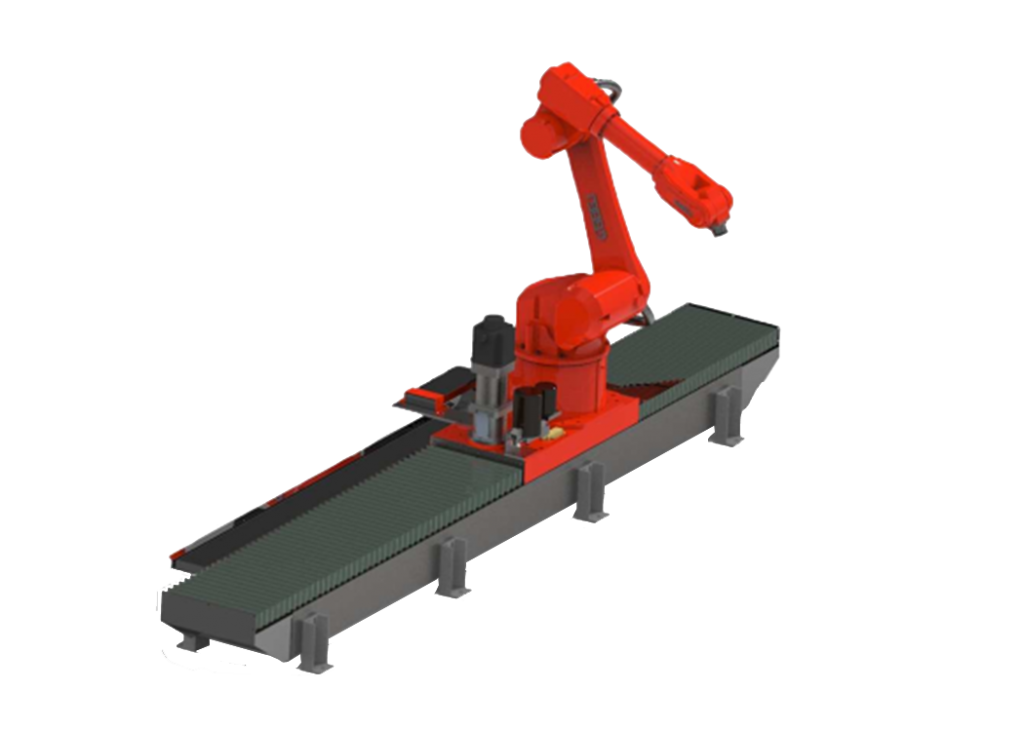
Linear Moving Rack
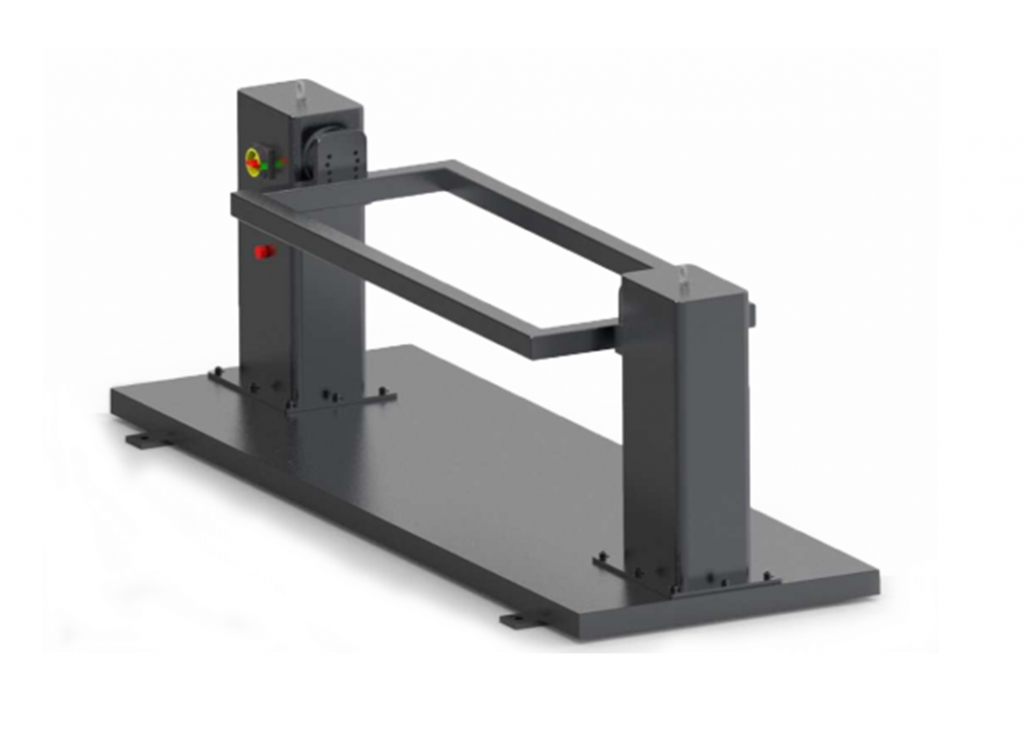
Welding Positioner

Torch Cleaning Station
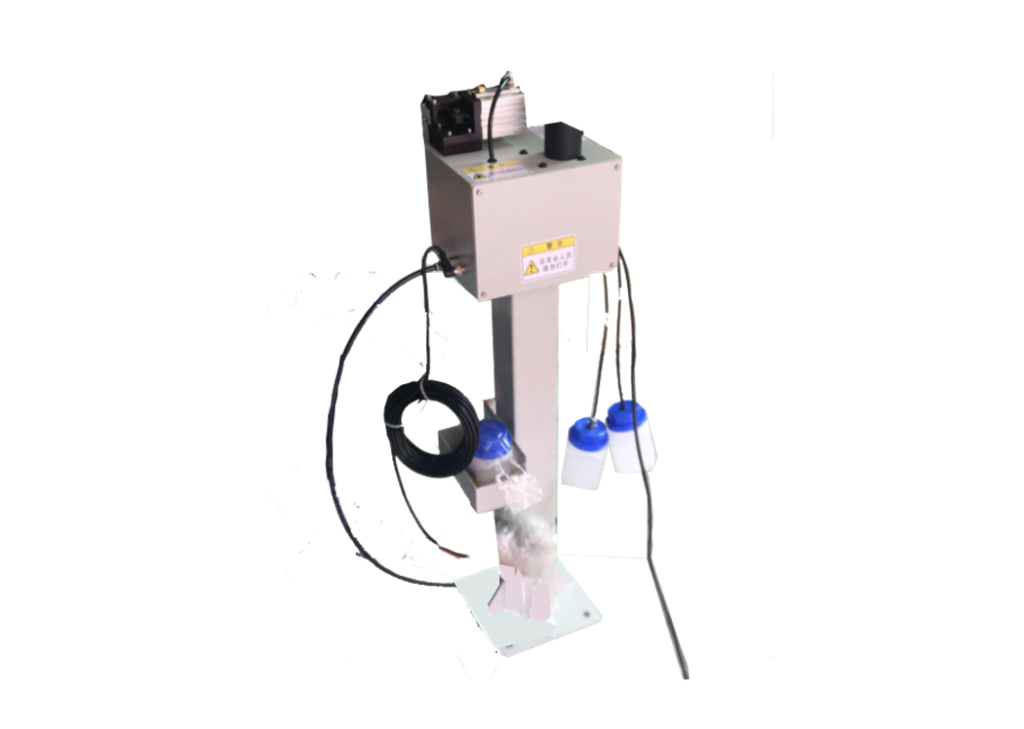
Water Cooling Device
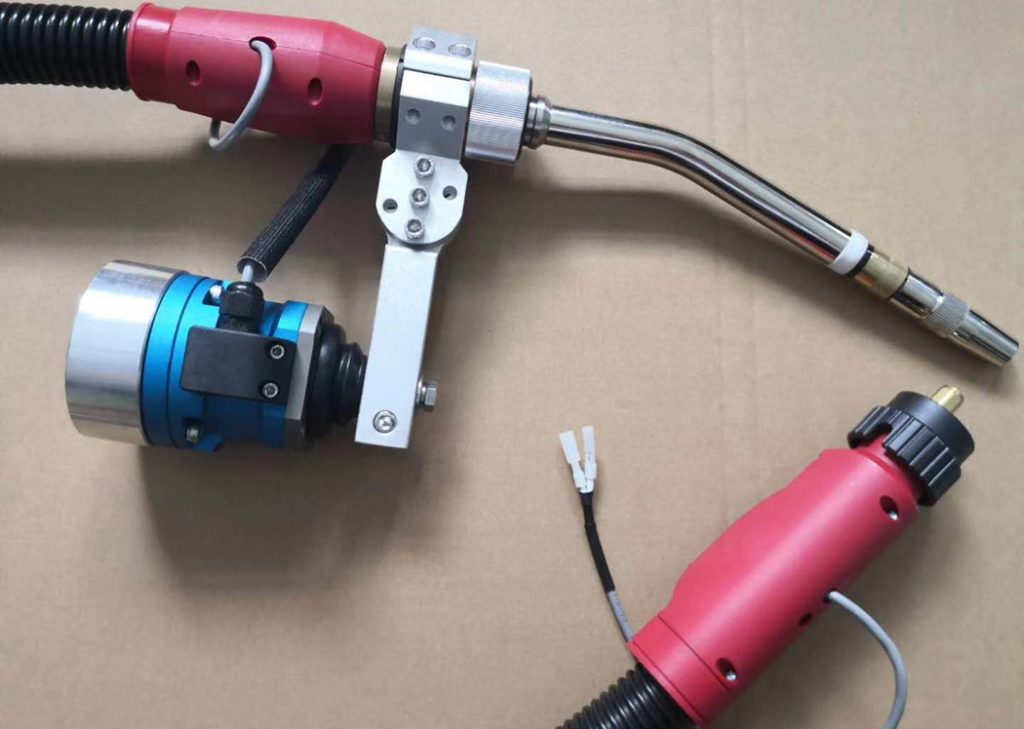
Welding Torch
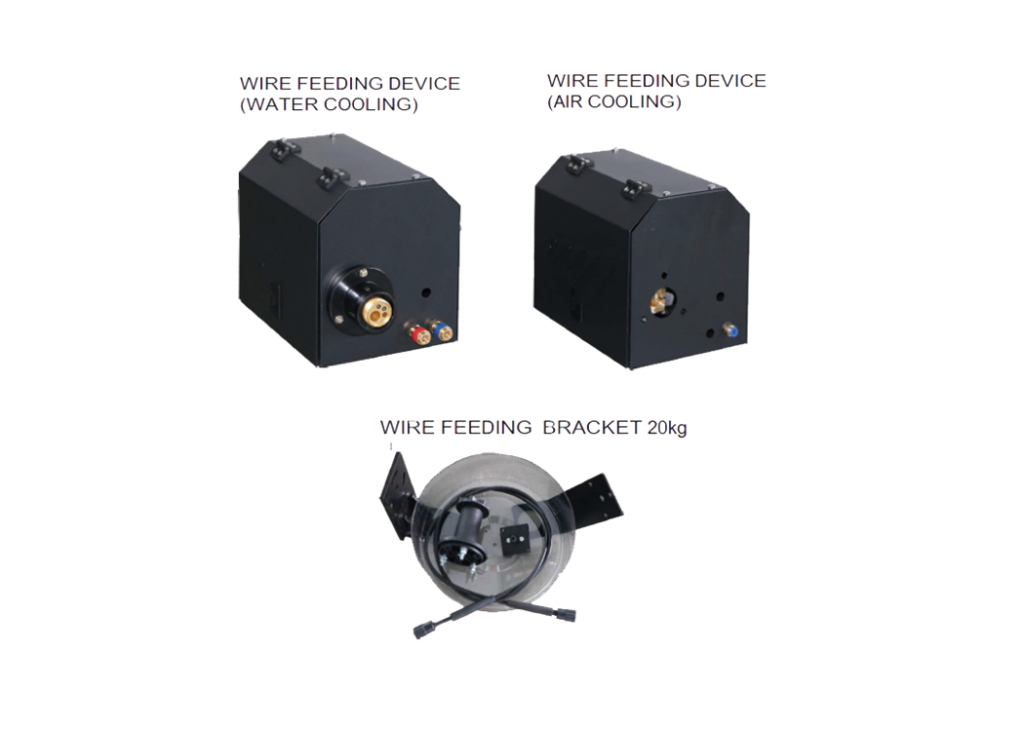
Wire Feeder
What Is MIG/MAG Welding Machine?
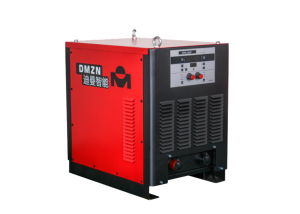
MIG sources used for robot and for aluminium alloy welding
The MIG/MAG welding machine is also an arc welding machine, but when the welding wire is consumed by welding, the coated electrode is replaced by the welding wire placed in the welding torch. In order to protect the electrode from oxidation caused by ambient air, the electrode coating is replaced by the gas released by the welding torch at the welding point.
MIG (Metal Inert Gas) welding uses an inert gas such as argon or helium. Suitable for stainless steel, light alloys and non-ferrous metals.
MAG (metal active gas) welding uses a mixture of argon and carbon dioxide or argon and oxygen, which reacts with welding, thereby improving welding quality. Only used for carbon steel.
When choosing the right gas, MIG/MAG welding can weld all common metals.
MIG/MAG welding machine produces better welding quality than MMA welding machine, can weld thinner sheets, and is more suitable for production, automation and robotics. MIG/MAG welding is also the easiest to learn.
The MIG welding machine can also be used without air supply. It is only necessary to replace the solid welding wire with a filler wire, and the filled wire will evaporate during the welding process to generate an inert gas protective layer, thereby protecting the weld from oxidation. MIG gas welding can achieve cleaner welding, solid wire is cheaper than filler wire, and gasless welding allows you to get rid of gas cylinder loading and unloading, and is less sensitive to airflow, so it is more suitable for outdoor work. It can also make the weld better penetrate into thicker materials.
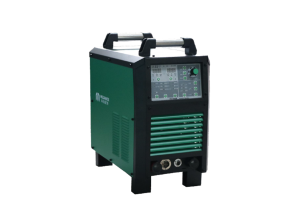
MIG welding sources special for robot
What Is TIG Welding Machine?
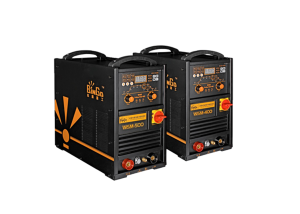
TIG welding source for stainless steel
TIG welding machine uses inert gas, non-melting electrode and filler metal. In some cases, welding can be performed without filler metal. The TIG welder is used to weld thin layers.
The TIG welder can be manual (the welder holds the auxiliary metal rod with his other hand) or semi-automatic (the welder is equipped with a reel for filler metal). This process is mainly used for non-ferrous metals such as titanium or aluminum. If filler metal is required, coating is not necessary because the welding area can be protected from corrosion by inert gas. This type of welding is very popular because it allows you to obtain high-quality welding results, especially in tight welding or thin metal plate welding.
The TIG welder needs cooling. For low welding strength, the cooling provided by gas is sufficient, but for higher strengths, a liquid cooling torch is required.
The electrode can be made of tungsten or a tungsten alloy, depending on the metal to be welded. The electrode is non-meltable (not helpful to the filler metal in welding), but it will still wear out and must be polished regularly because the quality of the arc depends on the shape of its tip.
- High performance verified over 10000 perfect weldling application for 12 years
- Robot controller adopting double system provides ten times of response speed than traditional.
- Rich terminals: 40 I/O
- Up to 5 external axis control,don’t need separate external controller,thus save money and installation space.
- Isolated transformer of welding robots as standard confiuration reduces external disturbance sharply.
- Dedicated welding application program free of charge, easy and friendly for user who can complete welding project programming quickly.
- Bus communication basaed on Modbus TCP/IP, RTU
- Anti-collision function
1) Maximize the protection of personal safety and prevent injuries caused by robot collisions,
2) Avoid position deviation arising from robot collision,
3) Avoid position deviation caused by welding wire sticking during the welding process
- Adopt worldclass products of RV gear,harmonic gear and servo
- Support color customized of robot arm
- Support delivery without robot logo
- Full technical support and response in 24hours x7
- Stable spare parts supply
- Extremely high cost effective, you can take much less money and enjoy high quality welding services.